What is Factory Digitalization
Have you ever wondered how we can benefit from it
Factory digitalization through MES, ERP, and SCADA (Supervisory Control and Data Acquisition) systems can significantly benefit your business. MES manages and monitors the production process, ensuring smooth operations and saving time. ERP takes care of inventory, finances, and orders, organizing everything efficiently. SCADA helps control and monitor your factory's machines and processes, ensuring they work optimally. With these digital systems, you'll have real-time data at your fingertips, make smarter decisions, improve productivity, reduce costs, and achieve a well-organized factory that operates seamlessly. It's like having super smart assistants and a team of reliable experts, all working together to make your factory successful!
Can this really help us with our operations?
From basic to high-end factories, both can benefit from digitalization
1.MES (Manufacturing Execution System):
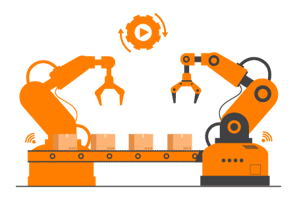
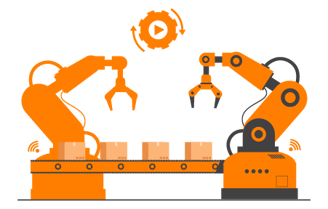
Streamlined Operations
MES helps organize and optimize manual processes, reducing downtime and enhancing production efficiency.
It enables real-time data collection and tracking of production activities, providing valuable insights into performance and areas for improvement.
Data Collection
Workforce Productivity
MES helps coordinate tasks and provides operators with clear instructions, leading to better productivity and reduced errors.
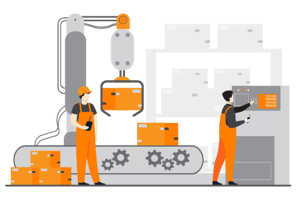

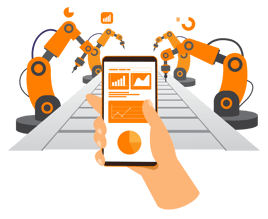
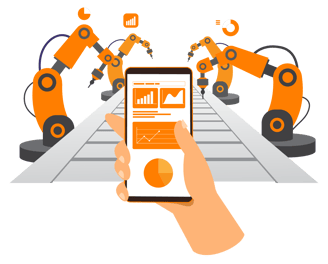
2.ERP (Enterprise Resource Planning):
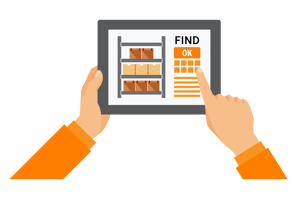
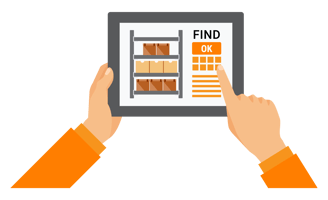
Inventory Management
ERP allows efficient tracking of raw materials and finished products, preventing stockouts and overstock situations.
It helps manage finances, costs, and budgets, improving financial decision-making and cost control.
Financial Visibility
Order Management
ERP streamlines the order process, ensuring timely fulfillment and customer satisfaction.
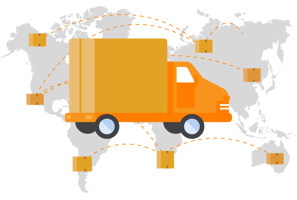
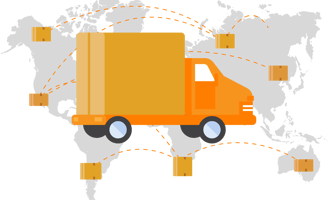
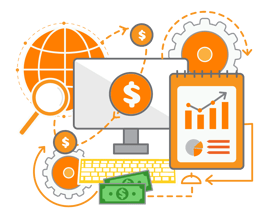
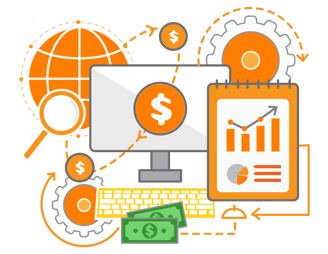
3.SCADA (Supervisory Control and Data Acquisition):
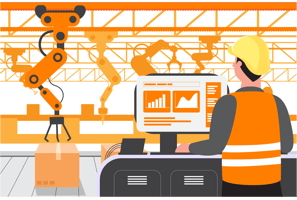
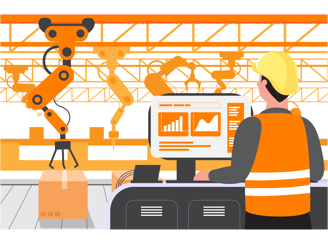
Process Monitoring
SCADA allows real-time monitoring of manual machines, detecting anomalies, and helping operators respond promptly to issues.
SCADA provides remote access to control and adjust machine settings, reducing the need for manual intervention.
Remote Control
Data Visualization
It presents data in graphical formats, making it easier for operators to understand and act upon critical information
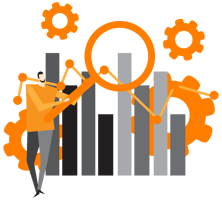
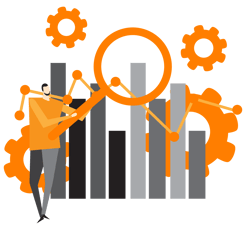
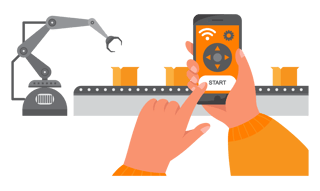
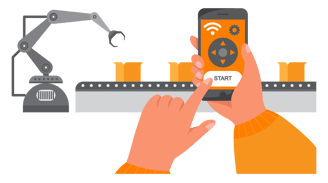
How others usually start their digitalization adoption?
Here are the typical process of factories adopting digitalization into their operation
1. Study the process flow
First, we carefully study how things are currently done in the factory. We look at each step of the production process, from raw materials to the finished product, to understand how everything works.
2. Find the chokepoint (most problematic area)
We identify the area that causes the most problems or slowdowns in the factory. It could be a specific machine, a manual process, or anything that hampers efficiency and productivity.
3.Propose the method of improvement
Once we know the problematic area, we come up with ideas to make it better. This could involve using new technologies, automating tasks, or finding smarter ways to do things.
4.Client agreement and sign off
We discuss our improvement ideas with the factory owner or management. If they like our plan, we get their agreement and approval to proceed.








5.System development / settings / customization / installation
Next, we start creating the digital system that will help implement our improvement plan. We set it up according to the factory's specific needs and customize it to fit perfectly.
6.System training & implementation
We teach the factory's staff how to use the new system effectively. It might take some time for everyone to get used to it, but we're there to support them during this phase.
7.System improvements and bug fixing:
After the system is up and running, we keep an eye on how it performs. If we find any issues or glitches, we quickly fix them to ensure everything works smoothly.
8.System go-live:
Finally, when everything is working perfectly, we officially launch the new digital system. Now, the factory can enjoy the benefits of increased efficiency, better productivity, and smoother operations.








A Journey into Digitalization for an Automative Factory
Let's take a look into how a typical automative factory would like to adopt automation into their processes
Step 1: Study the process flow
The digitalization team thoroughly examines the entire production process at the automotive factory. They observe how raw materials are received, how the assembly line operates, how quality checks are conducted, and how finished vehicles are prepared for delivery.
During their study, the team identifies that the inventory management and supply chain coordination are major challenges. There are frequent delays in receiving parts, leading to production interruptions and inefficiencies.
Step 2: Find the chokepoint (most problematic area)
Step 3: Propose the method of improvement
The team suggests implementing an ERP system that will integrate all aspects of the factory's operations. This system will automate inventory management, order processing, and supply chain logistics to ensure seamless coordination and timely availability of parts.
Step 4: Client agreement and sign off
The management of the automotive factory agrees with the proposed ERP implementation, recognizing the potential benefits in reducing delays, optimizing inventory, and improving overall production efficiency
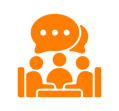

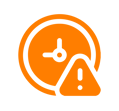

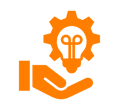

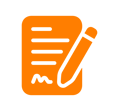

Step 5: System development / settings / customization / installation
The digitalization team collaborates with ERP experts to develop and customize the system according to the factory's specific requirements. They configure the system to handle automotive-specific processes, such as tracking individual vehicle components.
Step 6: System training & implementation
Factory employees receive comprehensive training on how to use the new ERP system. The team assists them during the initial stages to ensure smooth adoption and understanding of the system's functionalities.
Step 7: System improvements and bug fixing
After implementation, the team closely monitors the system's performance and gathers feedback from factory staff. They address any issues or bugs promptly, making necessary improvements to optimize system operation.
Step 8: System go-live
With the ERP system fully integrated into the factory's operations, the automotive factory experiences significant improvements. Inventory is now managed efficiently, ensuring an uninterrupted flow of parts. Production schedules are better synchronized, reducing delays and increasing productivity. The ERP system also generates insightful reports, enabling management to make data-driven decisions for further process enhancements.
As a result of this digitalization effort, the local automotive factory becomes more competitive, with streamlined operations, reduced costs, and improved customer satisfaction. The ERP system helps the factory respond more effectively to market demands, delivering high-quality vehicles on time, and positioning them for growth in the automotive industry.
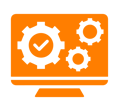

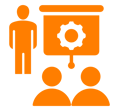

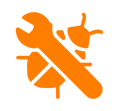

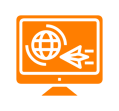

Is digitalization suitable for me?
Most factories are indeed ready, but they just don’t know it yet!
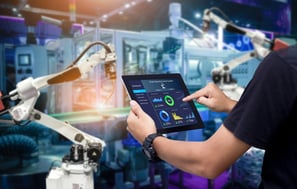
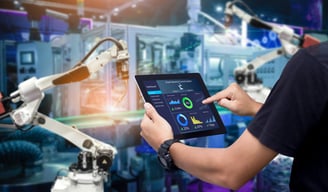
It enables real-time data collection and tracking of production activities, providing valuable insights into performance and areas for improvement.
Embracing change is essential too. Digitalization might mean introducing new technologies and adjusting how things are done, but it's worth it! With digital tools, you can analyze data, optimize processes, and make smarter decisions, all leading to increased efficiency and cost savings.
So, if you feel confident in your processes, have the data you need, and are open to positive changes, your factory is definitely ready for digitalization. It's like giving your factory a superpower boost, making it more competitive, efficient, and ready for a successful future!
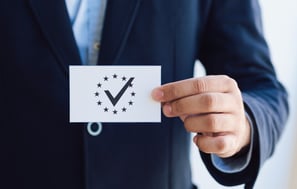
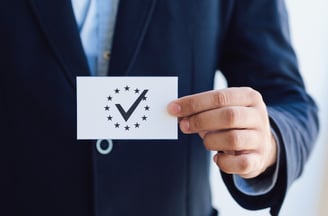
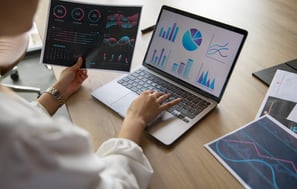
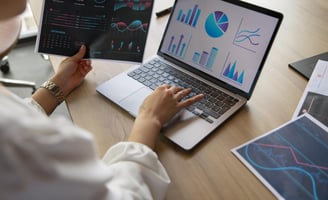
So, how can I start?
Lets dive into a typical process how it would look like for a factory to kick start their journey into digitalization
Congratulations on taking the first step towards digitalizing your factory! Here's what you can expect on your digitalization journey with MaDAMS:
We value your interest in MaDAMS, and we're eager to help you. Let's start by booking a free consultation session at your convenience. During this meeting, you can share your factory's challenges, and we'll listen carefully to understand your pain points.
Book a slot for FREE consultation:
We will study your pain points:
Our team of experts will conduct a thorough analysis of your factory's operations. By studying your pain points and current processes, we'll gain valuable insights into areas that need improvement.
Propose the most suitable MaDAMS module for your factory:
Based on our analysis, we'll suggest the best combination of MES, ERP, and SCADA modules customized to meet your factory's unique needs. The MES module will streamline production, the ERP module will optimize resources and finances, and the SCADA module will ensure efficient machinery control.
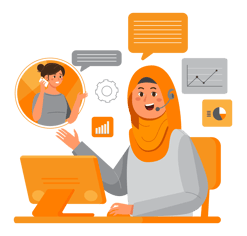
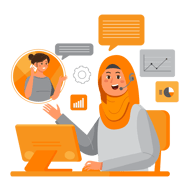
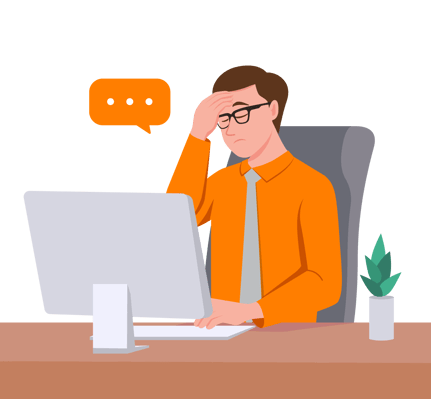
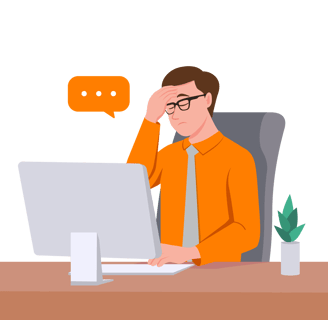
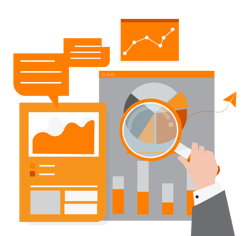
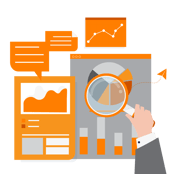
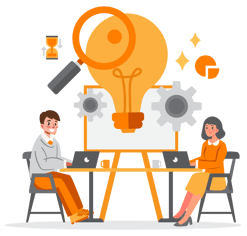
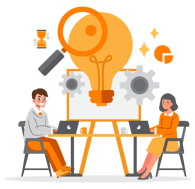
With MaDAMS, you can expect a guided digitalization journey that addresses your factory's specific challenges, enhances efficiency, and boosts productivity. Let's work together to unlock your factory's full potential and achieve greater success in today's digital era.
Looking forward to helping you transform your factory into a state-of-the-art, technologically advanced manufacturing hub!